Thus far, we only spoke about the first two types of process mining: process discovery and conformance checking.
In this lesson, we present the remaining two types: process enhancement and operational support. Both depend on process discovery and conformance checking results. We assume that we have an event log and a process model. The process model may have been discovered or partly made by hand. Using conformance checking, we can relate events in the event log to parts of the model.
Process enhancement, the third type of process mining, produces an improved or extended process model. For example, conformance diagnostics can be used to repair a process model to better reflect reality. This is particularly relevant if one would like to mediate between a model that people use or expect and the actual reality captured in event logs.
Another example is extending the model to show bottlenecks in the process. This can be done because events have timestamps, and we can replay them on the model. If activities have a start and complete event, then we can measure the difference and determine service times. Similarly, we can measure the time in-between activities. Even if we just have complete events, it is still possible to measure and visualize delays. For each bottleneck, we can show the average time, total time, minimal time, maximal time, and median time. We can also run a supervised learning algorithm to find out what delayed cases have in common.
The process model can also be extended with rules. For example, we can generate a decision tree for each choice in the process. The decision tree may reveal that cases handled by a particular employee tend to be rejected or that certain suppliers often change their prices leading to additional work. The idea is that the discovered process model shows all possible paths in the process, and decision mining is used to determine which factors influence the path chose.
The process model can also be extended with a resource or organizational information. There are process mining techniques that automatically discover work patterns, organizational roles, social networks, and scheduling mechanisms. These approaches use both the event log and the discovered process model. For example, we may discover that there are two teams handing different subsets of activities. One team handles things in a First Come First Served manner, and the other team handles things based on the due date of the case.
By combining all of these process enhancement techniques, it is possible to create a model that describes not only the ordering of activities, but also the time, data, and resource dimensions. This way, it is also possible to automatically create simulation models that answer "What if?" questions. Such simulation models can be seen as digital shadows of the real process. These digital shadows can be used to explore the anticipated effects of process changes, for example, making a sequential production process more concurrent or adding an additional assembly robot.
The fourth type of process mining is operational support. Operational support techniques use the extended models just described, to say something about still running cases. The focus of the techniques discussed before was on completed process instances. However, from a business point of view, the running cases are at least as interesting. Take, for example, conformance checking. It may be more valuable to generate an alert the moment a deviation takes place, rather than reporting deviations in the past. Another example of operational support would be to predict the remaining flow time of a running case or the likelihood of a system failure. By combining process mining with machine learning, it is possible to build predictive models for any type of future behavior. For structured processes with enough event data, it is possible to predict performance and compliance problems allowing for interventions. In fact, based on good predictive models, it is easy to provide recommendations. Automatically generated recommendations may guide the user in selecting the next activity or trigger management to increase capacity before the bottleneck emerges.
Operational support and process-mining-based simulation and machine learning techniques are forward-looking. However, such techniques can only be used when the process is structured and in a steady-state. For unstructured and constantly changing processes, the more backward-looking techniques are more valuable. For processes that are unstructured, basic process discovery results already reveal a lot of low-hanging fruit to improve the process.
I hope that by now, you realize how broad the field of process mining is and that it can be applied to any operational process: structured or not. However, process mining is only possible when we have suitable event data. In the next lesson, we focus on getting the event data needed to do process mining.
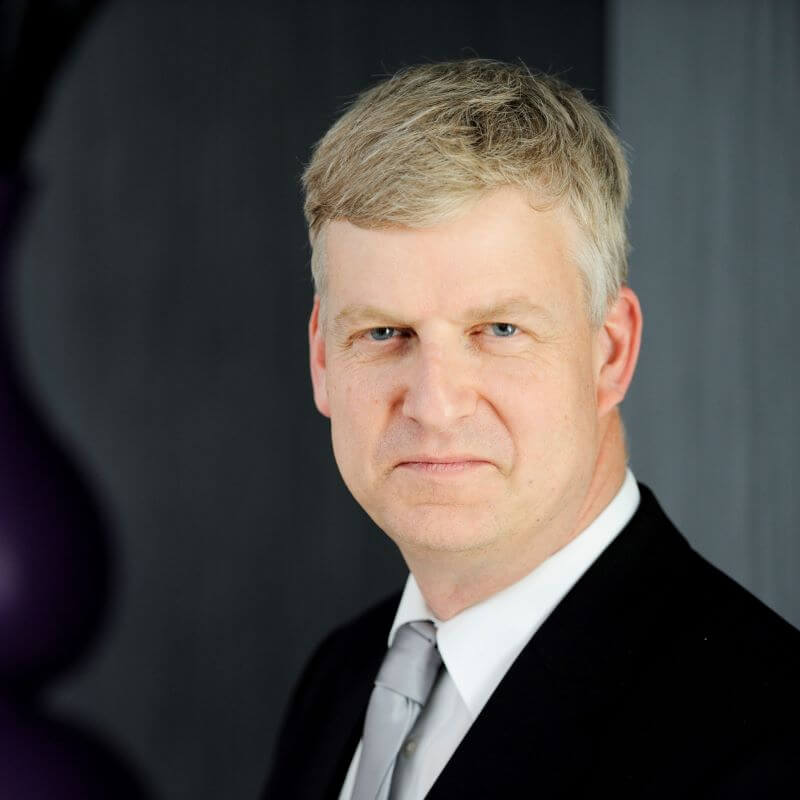